
_2.jpg)
High operating costs make their use somewhat prohibitive in the utility installation market, and they are employed primarily in the pipeline industry. Maxi rigs typically involve a large operation with multiple trailer-mounted support equipment and substantial mobilization and demobilization periods. Many of the drill rigs in this class are self-contained units. Bores can be installed in unconsolidated to consolidated sediments.
HDD DIRECTIONAL DRILLING INSTALL
They are particularly suitable for the installation of municipal pipelines, as they are sufficiently compacted to be used in urban areas while at the same time they have the capacity to install large-diameter products beneath highways, subdivisions, andįIGURE 1-4 Typical HDD Rig TABLE 1-3 Typical Characteristics of HDD Rigs Medium-sized drilling rigs are used to install larger conduits and pipelines, normally up to 16-inches in diameter, with drill lengths ranging up to 2000 feet. The higher end of this class of drill rigs is suitable for drilling in gravel and cobbles as long as the bore lengths are not excessive. They are not suitable for drilling gravel, cobble, or other formations where bore-hole stability is difficult to maintain. The lower end of this class of drill rigs (less than 20,000 pounds thrust/pullback) is designed for drilling in relatively soft semiconsol-idated formations and is used primarily for the installation of utility conduits and small-diameter pipelines in congested urban areas. The self-propelled units are self-contained, with the engine, hydraulic power, and drilling fluid pump all part of the unit. Mini rigs are mounted on a trailer, truck, or self-propelled track vehicle. Table 1-3 lists the three general categories of drilling rigs used in the industry. The thrust mechanism for the carriage can be a cable, chain, screw, or rack-and-pinion system. The drill drive assembly resides on a carriage that travels under hydraulic power along the frame of the drill rig. HDD drill rigs provide torque, thrust, and pullback to the drill string. The HDD drill rig is used to drill and ream the pilot hole and pull the product pipe back through the hole. Maximum volume of drilling fluid a machine can pump per minute, and spindle revolutions per minuteĪ typical HDD rig is illustrated in Figure 1-4.Thrust and pullback force, stated in pounds.
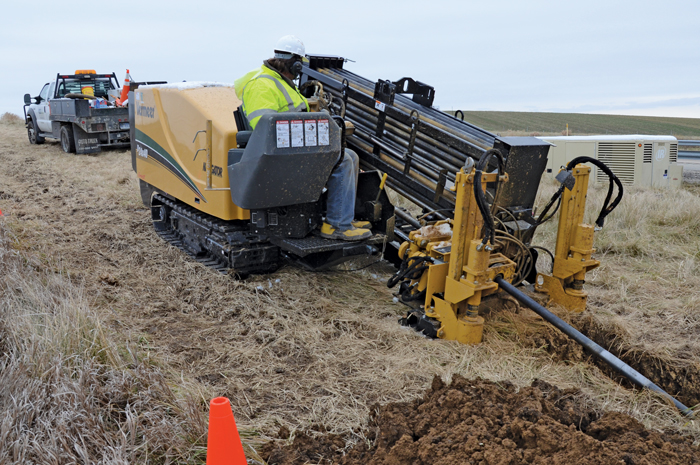
This includes ensuring that appropriate types and quantities of drilling fluids and additives are on hand. Ensure that all the equipment and material required for the HDD project are on hand and in good condition. HDD entry and exit points, should well marked in accordance with the project plans and specifications. The project area, including theġ0 Chapter 1 ■ Introduction to Horizontal Directional Drilling The HDD rig is often tied down using the powered rotating screws located on the front of the drill rig. Fluid recirculating systems often are employed on long bores to install large-diameter pipe.Īfter offloading the HDD rig, it is positioned over the bore path centerline at an adequate distance from the drill entry point to allow the drill bit to enter the ground at the desired location and angle. The fluid mixing system is separate from the drilling rig. The drilling fluid, commonly known as mud, plays an essential role in drilling, back reaming, and product pullback. Back reamers are used to increase the diameter of the pilot hole to the required size to accommodate the diameter of the pipe to be installed. The HDD rig is connected to the cutting bit by the drill string, which is made up individual joints of pipe. Drilling fluid mixing or recycling system.Drill pipe and downhole tools, including bits and back reamers.Horizontal Directional The basic components of a horizontal directional drilling system include:
